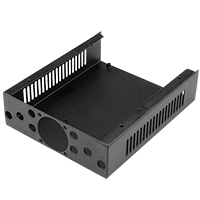
CNC Machining
From prototype design to mass production, milling, turning, and drilling empower precisely.
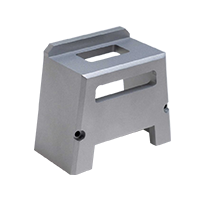
Mechanic Design
Conquer the challenges of Product ID and professionally create 3D drawings for appearance and structure.
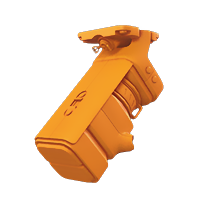
Replication Molding
Small - batch prototyping processing is available. We offer one - stop surface treatment services including painting and silk - screening.
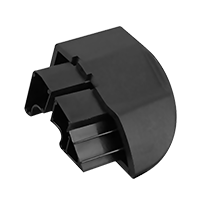
Injection Molding
With diverse techniques such as overmolding, insert molding, and two - color injection molding, mass production is achieved.
Product design and professional processing services
A flexible online trading platform for small-batch prototyping and processing, specializing in structural design, 3D printing, CNC machining, molds, and injection molding, focusing on high quality and efficiency in production.
Mechanic Design
Appearance design solves the problem of product ID. From appearance to structure, experienced structural engineers are required to analyze and make proposals Make files for 3D print\CNC\Molding.
3D Printing Services
Utilize industrial-grade UV cured 3D printing services to achieve high-precision and high-temperature resistant printed samples. Support various surface treatments, making it the ideal choice for new product validation or sample display.
CNC Machining
Equipped with a variety of CNC machining centers, With a variety of specifications of CNC equipment, solid line high-precision sample proofing and parts processing; Support a wide range of materials and surface treatment services
Silicone Coated
Silicone rapid molding is the optimal method for small batch and low-cost market testing. It supports a variety of materials and surface treatments. Silicone rapid mold, small batch low-cost market test the best way
Injection Molding
Our experienced mold development team provides professional services from mold design to manufacturing. Additionally, we offer injection molding processing to realize a one-stop service from design to mass production.
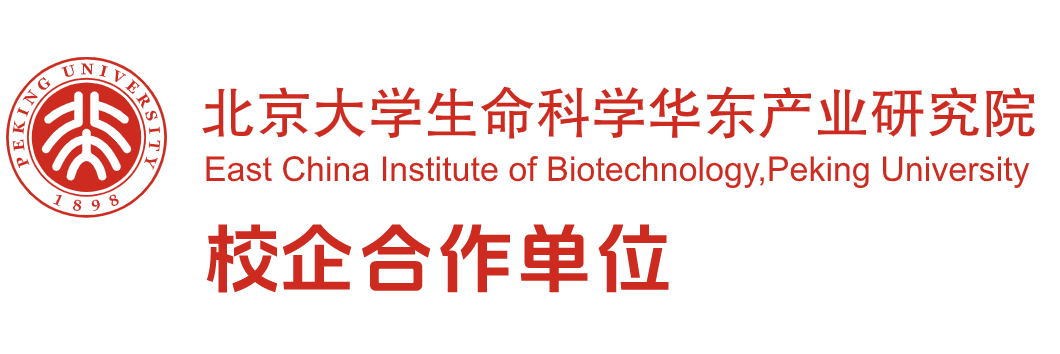
MOMAKING Using AI industry models to drive technological innovation in part modeling.
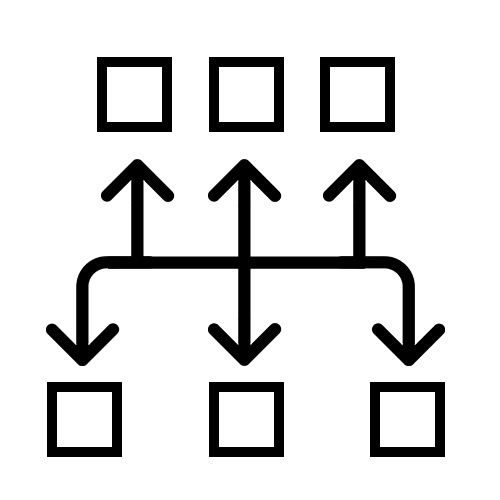
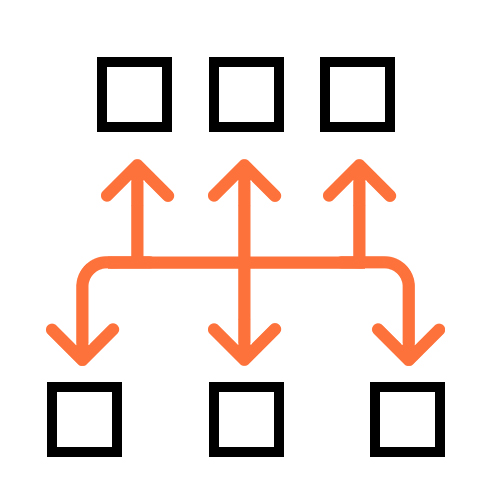
A factory of continuously refined manufacturing.
Momaking's factories are located in Shenzhen Shiyan, Dongguan Changan, and Zhongshan Guzhen. With a strong talent base in Shenzhen and the advantages of Dongguan Changan's mold industry, along with the cost benefits of the Zhongshan factory, we achieve high quality at low cost. Our professional talent, industrial linkage, and efficient manufacturing bases allow us to offer one-stop services including structural design, 3D printing, CNC machining, mold manufacturing, and injection molding.
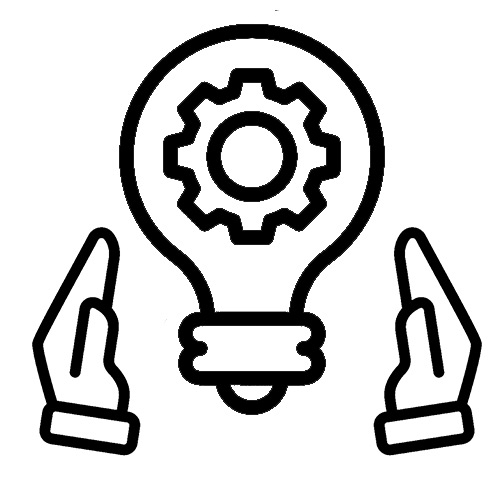
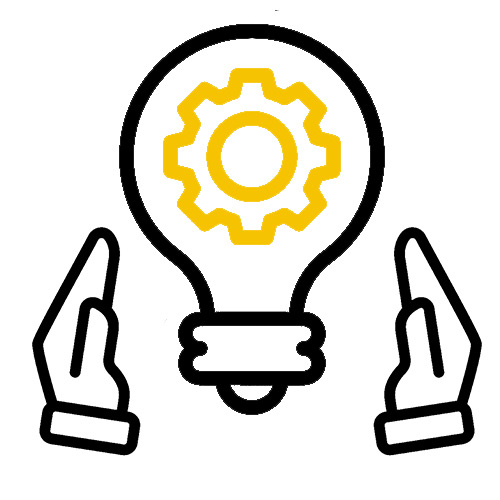
AI-driven Real-time Quotation System
By investing heavily in an AI team, we developed an AI model for precision processing that calculates costs for various drawings in seconds. This eliminates the wait and replaces inefficient traditional methods reliant on personal connections or instant messaging for pricing. Integrating AI into foundational industries enhances efficiency, reduces management costs, and achieves high-quality, cost-effective outcomes.
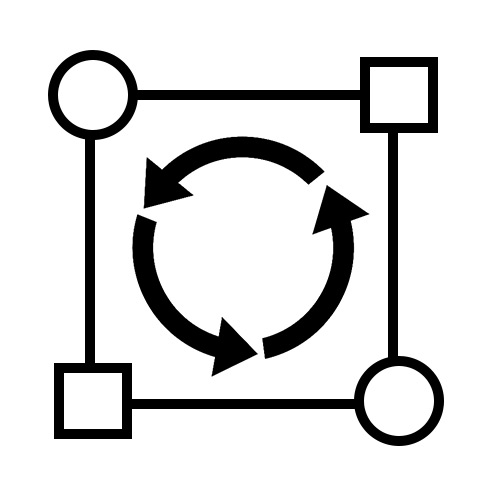
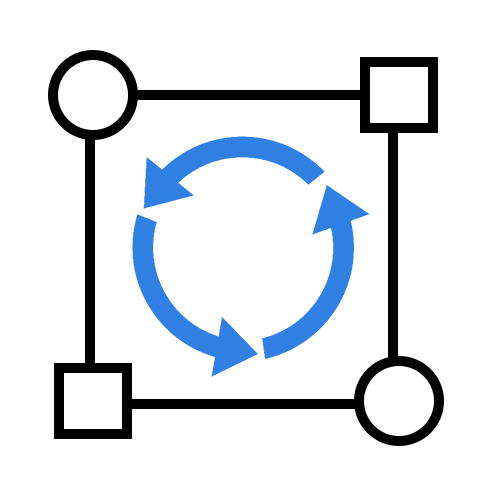
Full Chain Visualization Process
Adhering to a strict confidentiality system, we maximize the OA digitalization of the entire chain of processes to the greatest extent possible, significantly limiting access to drawings by unnecessary personnel. With full OA digitalization of the chain, each link operates according to the prescribed manufacturing process and stringent quality standards, providing real-time updates on the status of part processing. This ensures a secure, high-quality, and efficient delivery with precise and timely accuracy.
Your AI-Powered Real-time Quotation
Upload your 3D file, select materials, processes, and surface treatments.
Industry-leading billion-parameter model, precise and fast quoting.
Place your order online with a fully transparent view of the process fees, without any additional hidden costs.
Convenient and Quick Quotation Process
2.Wait for the AI analysis model to process the file.
3.Modify the technology or material if needed.
4.Submit your order or have it reviewed by a person.
News Center

On Demand 3D Printing Service: Is It More Cost-Effective?
Cost plays a role in decision-making within the manufacturing industry. In the realm of manufacturing when weighing metal 3d printing services, against manufacturing approaches.
2025-03-18 10:04:57
How Five Axis CNC Machining Enhances Efficiency in CNC Machine Centers
The advent of five-axis CNC machining has brought about computer numerical control (CNC) technology much beyond the conventional three-axis machines
2025-03-12 10:38:52
Navigating the Complexities of Rapid Prototyping with 3D Printing Services
The prototyping process has transformed the product design and sale in the market to a great extent
2025-03-10 11:09:12
How Part Placement Affects SLS 3D Printing Quality and Strength
Discover how part placement in SLS 3D printing impacts surface smoothness, strength, and accuracy. Momaking's industrial-grade machines optimize results.
2025-06-30 18:46:57
Custom Resin Miniatures: A Gamer’s Go-To Guide for 3D Printing
Discover how to design and print custom resin miniatures with high detail and fast turnaround.
2025-06-27 18:46:28
Making Plastic Injection Molding Faster and More Efficient
Discover proven strategies to speed up plastic injection molding cycles, reduce costs, and boost quality. Learn tips on mold design, automation, and materials.
2025-06-27 18:40:40